La prima linea di rivestimento celle dello stabilimento di Lipsia del Gruppo BMW è entrata in funzione in serie mentre la produzione di componenti elettronici nel sito continua a guadagnare slancio.
Entro il 2024 le due linee di assemblaggio dei moduli esistenti saranno integrate da una terza, oltre ad altre quattro linee di rivestimento delle celle e altre due linee di assemblaggio di batterie ad alta tensione. Le quattro linee di rivestimento entreranno in esercizio in serie nel corso di quest’anno a intervalli di circa due mesi.
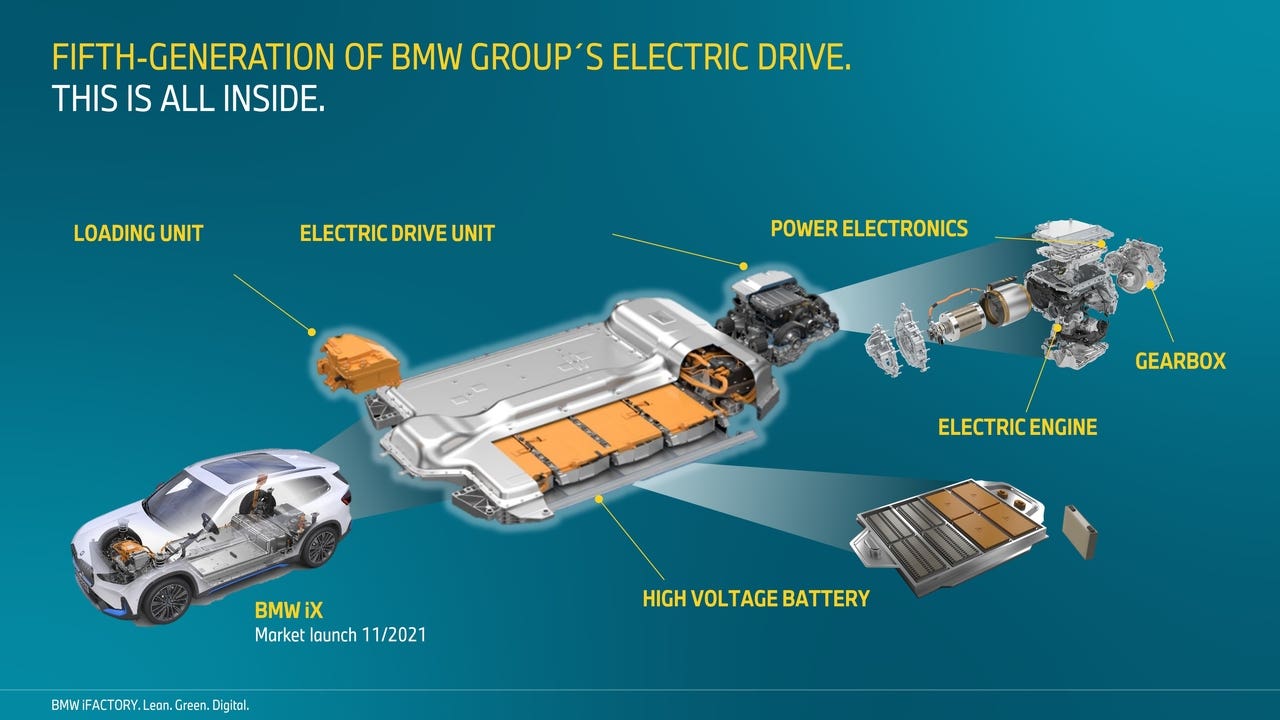
BMW: partita la produzione del rivestimento celle presso lo stabilimento di Lipsia
Markus Fallböhmer, responsabile della produzione di batterie del BMW Group, ha detto che, dal 2024, la fabbrica tedesca sarà in grado di gestire l’intera catena di processo per la produzione di batterie ad alta tensione. Quindi darà un contributo importante alla trasformazione verso l’elettromobilità.
Per raggiungere il suo obiettivo di veicoli completamente elettrici che rappresentino almeno la metà di tutte le vendite entro il 2030, il colosso tedesco dell’automotive sta investendo oltre 800 milioni di euro per stabilire e sviluppare la produzione di componenti elettronici presso l’impianto di Lipsia.
Con una superficie di 2300 m², il nuovo sistema di rivestimento delle celle presente presso la fabbrica di Lipsia si trova nell’ex capannone di produzione della BMW i3, dove l’assemblaggio è stato gradualmente interrotto nell’estate dello scorso anno. Subito dopo lo spazio è stato convertito per la produzione di componenti elettronici in meno di sei mesi e i dipendenti hanno seguito la relativa formazione.
La nuova linea di rivestimento è in grado di gestire più di 10 milioni di celle all’anno, ovvero oltre 2300 all’ora. Le celle rivestite vengono quindi utilizzate sulla linea di produzione dei moduli batteria a Lipsia per realizzare le batterie delle i4 e iX1 completamente elettriche. Un’altra linea della struttura sta producendo batterie per il BMW iX.
Ecco come è strutturata la produzione delle batterie
La produzione delle batterie avviene in tre fasi: rivestimento delle celle, produzione dei moduli e assemblaggio della batteria stessa. I processi sono altamente automatizzati.
Il Gruppo BMW acquista le sue celle da partner che le producono esattamente secondo le specifiche. Il tipo utilizzato dipende dal veicolo interessato ed è scelto per garantire le migliori caratteristiche possibili.
Il rivestimento delle batterie agli ioni di litio consiste innanzitutto nel pretrattare e modellare le loro superfici con un laser. Ciò implica che il raggio laser “scalpella” una struttura all’esterno della cella non rivestita per aumentarne l’area superficiale e ridurre la tensione superficiale dell’involucro di alluminio. Successivamente, le celle vengono pulite per rimuovere eventuali particelle di sporco e ossidi.
Insieme, questi due processi migliorano l’adesività della superficie, pronta per l’applicazione del rivestimento. Viene somministrato da una macchina appositamente sviluppata che riveste le celle in due strati, che vengono poi induriti dai raggi UV e offrono il miglior isolamento possibile per le celle.
Infine, viene eseguito un processo di controllo qualità in tre fasi completamente automatizzato in cui vengono ispezionati lo spessore e la qualità della superficie del rivestimento. Viene condotto un test ad alta tensione per garantire che il rivestimento sia completamente privo di difetti.
Il rivestimento delle celle utilizzato dal gruppo automobilistico tedesco è il blu, scelto deliberatamente per il suo ruolo importante nel posizionamento dei veicoli elettrici BMW i e come colore identificato della gamma elettrica.
All’interno della rete di produzione del gruppo, lo stabilimento di Lipsia è pioniere dell’elettromobilità, avendo prodotto la i3, il primo modello completamente elettrico dell’azienda, dal 2013 al 2022.
La produzione di componenti aumenterà sempre di più
Una volta rivestite, le celle della batteria vengono assemblate in unità più grandi note come moduli. Una volta completati, vengono inseriti in un alloggiamento in alluminio insieme alle unità di controllo e raffreddamento e ai connettori che li collegheranno al veicolo. Le dimensioni e la forma dell’alloggiamento e il numero di moduli all’interno dipendono dall’EV. In questo modo, ogni auto riceve la batteria più adatta.
La continua espansione dell’impianto di Lipsia è fortemente trainata dalla produzione di componenti elettronici, che in futuro occuperà circa 150.000 m² di spazio produttivo. Petra Peterhänsel, direttore dello stabilimento, ha affermato che si tratta di un investimento a lungo termine nel futuro della fabbrica tedesca.
L’ampliamento dello stabilimento non solo salvaguarderebbe i posti di lavoro esistenti, ma ne creerebbe anche di nuovi. Attualmente, più di 800 persone lavorano nella produzione di componenti elettronici a Lipsia. Entro il 2024 ce ne saranno più di 1000.
La prossima grande pietra miliare per questo impianto sarà la produzione del successore della Mini Countryman, che uscirà dalle linee di produzione a partire dalla fine di quest’anno. Il crossover sarà disponibile con una scelta di motori a combustione intera o 100% elettrico con batterie prodotte sempre a Lipsia.